Strategies for Streamlining Corporate Furniture Storage Logistics
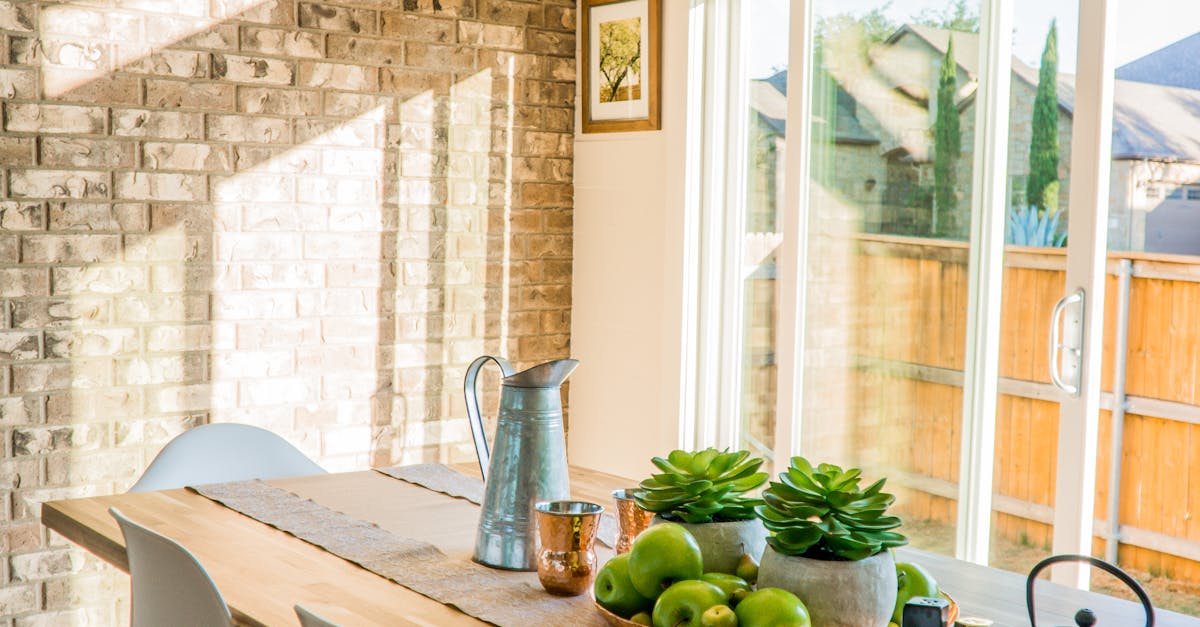
Table Of Contents
Regular Maintenance and Inventory Checks
Maintaining an organised and efficient storage space requires regular inventory checks. This practice allows businesses to keep track of furniture quantities, identify items that are no longer needed, and ensure that everything is in good condition. By establishing a scheduled routine for these checks, companies can proactively manage their resources and alleviate the risk of over-stocking or running out of essential items. Such diligence in monitoring inventory can lead to cost savings and improved space utilisation.
Scheduling regular maintenance of furniture is equally vital to prolonging its lifespan. Periodic inspections help identify wear and tear, allowing for timely repairs or replacements before they become more significant issues. By ensuring that furniture is well maintained, organisations can uphold their professional image while avoiding unexpected expenses due to damage or the need for rapid acquisitions. An effective maintenance plan fosters a more functional workspace while supporting overall operational productivity.
Establishing a Routine Inspection Schedule
Regular inspections of furniture storage areas are essential for maintaining an organised and efficient logistics operation. This process helps identify wear and tear on items that may require repairs or replacements. Scheduling these inspections at consistent intervals can prevent larger issues from arising, ultimately saving time and costs in the long run. It is advisable to document findings during each inspection to track trends and address recurring problems effectively.
Creating a routine inspection schedule involves setting specific dates and assigning responsibility to team members who are trained in evaluating the condition of stored furniture. Utilising checklists can streamline the process, ensuring that all relevant aspects are covered each time. Involving staff in the scheduling of inspections can foster a sense of ownership, encouraging everyone to prioritise the upkeep of storage spaces. Regularly reviewing this schedule helps adapt to changing needs and improves overall operational efficiency.
Staff Training for Efficient Logistics
Training staff in logistics is essential for improving efficiency and productivity in furniture storage. Employees should be well-versed in the specific handling techniques for different types of furniture. This includes understanding weight distribution and the best methods for lifting and transporting items to prevent damage. Regular workshops can help reinforce this knowledge while fostering a culture of safety and responsibility among the team.
Incorporating technology into training can further enhance logistics operations. Familiarising staff with inventory management systems ensures accurate tracking of available stock. Additionally, using digital tools for data entry and reporting streamlines communication across teams. As employees become more proficient in these systems, it reduces the likelihood of errors and improves overall workflow in furniture storage and retrieval processes.
Best Practices for Handling and Storing Furniture
Proper handling of corporate furniture begins with understanding the specific requirements of each item. Heavy office desks should be lifted rather than dragged to prevent structural damage. For delicate items, such as glass conference tables, it is crucial to ensure they are protected with padding during transport. Utilising appropriate tools like dollies or carts can significantly reduce the risk of injury and damage. Team members should communicate effectively while moving furniture to navigate tight spaces safely.
When storing furniture, maintaining a clean and organised environment is essential. Items should be stored off the ground on pallets or shelves to avoid exposure to moisture. Labeling storage areas can help staff quickly locate specific pieces and avoid unnecessary movement. Ensuring that furniture is covered with protective materials prevents dust accumulation while mitigating the risk of scratches or dents. Implementing these practices will facilitate smoother operations and preserve the integrity of the furniture over time.
Emphasising Sustainability in Storage
Sustainability has become a cornerstone for many organisations seeking to enhance their corporate responsibility. Incorporating eco-friendly practices in storage logistics can significantly reduce the environmental impact of furniture storage. Using sustainable materials for packing and storage solutions contributes to a greener footprint. Choosing recycled or biodegradable options not only lowers waste but also sets a precedent for corporate social responsibility.
Implementing energy-efficient systems in storage facilities aids in minimising electricity consumption. This can involve using LED lighting, optimising HVAC systems, and utilising renewable energy sources where possible. Organisations can also benefit from partnerships with local charities to donate unused furniture, promoting reuse and recycling while benefiting the community. These strategies not only enhance sustainability but also improve the overall efficiency of furniture storage operations.
Eco-Friendly Practices for Corporate Logistics
Incorporating sustainability into corporate furniture storage logistics contributes to environmental conservation while often reducing costs. Using recycled materials for packaging and promoting the reuse of furniture can significantly minimise waste. Companies can also explore partnerships with organisations that specialise in recycling office furniture, ensuring that items no longer in use are responsibly disposed of or repurposed.
Additionally, investing in energy-efficient storage solutions can lower utility expenses while reducing the carbon footprint. Modern storage facilities equipped with LED lighting and smart climate control systems enhance energy efficiency. Adopting digital inventory management systems not only streamlines operations but also decreases paper usage, aligning with eco-friendly practices throughout the logistics chain.
FAQS
What are the benefits of regular maintenance and inventory checks for corporate furniture storage?
Regular maintenance and inventory checks help ensure that furniture is in good condition, prevents potential damages, and allows for accurate tracking of assets, leading to more efficient storage logistics.
How often should we conduct inspections of our furniture storage?
It's recommended to establish a routine inspection schedule, typically every six months or quarterly, depending on the volume of furniture and the frequency of its use.
What training should staff receive to improve furniture handling and storage?
Staff should be trained on best practices for handling furniture, including proper lifting techniques, safe storage methods, and the importance of maintaining inventory accuracy.
What are some best practices for handling and storing corporate furniture?
Best practices include using appropriate equipment for lifting, ensuring items are stored in a way that minimises damage, and maintaining clear pathways for easy access to stored items.
How can we incorporate sustainability into our furniture storage logistics?
Incorporating sustainability can involve eco-friendly practices such as recycling old furniture, using sustainable materials for storage solutions, and optimising storage space to reduce the overall footprint.
Related Links
Comparing Traditional vs. Modern Corporate Furniture Storage OptionsHow to Securely Store High-Value Corporate Furniture
Key Features to Look for in Corporate Furniture Storage Services
Understanding the Costs Involved in Corporate Furniture Storage
The Role of Corporate Furniture Storage in Office Downsizing
A Guide to Selecting the Right Corporate Storage Facility